| Length Graders | Split Cylinder Length Graders | Rotary Screen Cleaners | Aspirators | Destoners | Threshers | Combo Cleaners | Indent Cylinder Length Separations | Scalper Aspirators |

Length Graders
Crippen Indented Cylinder Length Grader
The Crippen Indented Cylinder Length Grader is extremely accurate. To determine separations of product by product length, the Crippen Length Grader simply lifts the shorter product out of the longer product of the main product flow that enters the cylinder intake end. These machines can be stacked in to multiple banks to achieve any desired capacity, most commonly from 100 to 2000 Bu/hr (2.7 to 55 MTPH).
​
These machines can be arranged in a “Series Flow” or “Parallel Flow” arrangement. The “Series Flow” is arranged to make multiple separations of an incoming product flow in a common bank of cylinders. A common example would be removing both small weed seeds and long trash or wild oats from a good wheat product flow. The “Parallel Flow” arrangement is simply multiple cylinders in a common bank performing the same product separation, such as removing short or cross-broken kernels from a good long-kernel rice product flow. The Crippen Indented Cylinder Separator is an ideal machine to have in the processing of any product that has a difference in product lengths.
​
Features
-
Exclusive Tapered Cylinder Design for Positive Cleanout
-
23″ Diameter × 88″ Long Separating Cylinders
-
Crippen Quick Change Cylinders Standard
-
Hardened Cylinders Standard, the Hardest in the Industry
-
Sealed Friction Rollers Standard
-
Highest Quality Sealed Roller Bearings Standard
-
Sprocket and Chain Drive Standard
-
TEFC 3ph/60hz/230-460 volt Motors
-
Optional Direct Drive with VFD Controller to Adjust Cylinder Speeds
-
Optional Mechanical Hi-Lo Drive to Adjust Cylinder Speed
-
Modular Design Allows Machines to Be Stacked
-
A Bank of Cylinders Consists of Multiple S-1 Machines Stacked on Top of One Another
-
A Single Bank May Be Stacked as Many as Five Cylinders High
-
Each Bank May Be Stacked as Wide as the Application Requires
​

Applications For The Crippen S1 And S1-QC
Hybrid Corn Plants
The Crippen length grader is exceptionally efficient at separating hybrid seed into various lengths. The special features of the Crippen machines result in greater accuracy. Various height arrangements may be set to re-run either the liftings or the rejects.
Rice Mills
The Crippen machine is used in rice mills to grade clean rice. The cylinders may be installed in banks of various heights to obtain all the necessary separations for grades from extra fancy to brewers. The machines may also be furnished with indent cylinders to lift shelled or clean rice from paddy rice in rough cleaning in seed warehouses.
Flour Mills
The Crippen S1 and S1-QC is recommended for use in all flour mills. Installed in banks of various heights, the Crippens obtain optimum separations and capacities. They may be used particularly to reclean wheat from oat tailings from other equipment.
Oat Cereal Plants
The Crippen graders can be equipped with indent cylinders to separate oats into various lengths, removing the pin oats before the products go to the hullers. They can be supplied in many height arrangements.
Grass Seed Processors
The Crippen length graders are extremely popular in the world for removing longs and shorts from good grass seed. Again, through the use of varying height arrangements, proper sizing can be done efficiently and easily.
Sunflower Processors
In the Sunflower Industry, the Crippen S-1 is used to remove unwanted long trash such as sticks and stems. The Crippen model is used by many processors to achieve the highest standards in quality cleaned sunflower products today.
Models

S-1-QC Grader

LGX-13 Grader

D22-2A Grader
Split Cylinder Length Graders
​
The Ideal LG Series can be installed as a single unit (LG-1) or stacked in banks. Stacked machines can be set up in parallel flow to increase capacity or in series flow for regrading purposes.
​
Seed enters the revolving indent cylinder and flows toward discharge end, and liftings drop free from the indents at a selected high point. A conveyor moves the liftings through the trough to the outside spouting. The longer seeds not being lifted, move through the indent cylinder to the “longs” discharge spout.

Rotary Screen Cleaners
​
Bjerke Brothers, Inc. continues to evolve by offering new and improved grain cleaning equipment for its global customer base. During the past few years, engineers at CNSSC have been busy designing a new era of rotary screen machines offering great capacity, versatility and improved performance.
​
Working by means of rotary motion, the new NS Series rotary screen cleaners have the ability to remove both small and large foreign material from a vast variety of grains, oilseeds and pulse crops. The superior rotation speeds on the NS rotaries allow for a maximum presentation of screen surface to grain and, therefore, much higher capacities than possible from conventional screen separators. Depending on the model and application, capacities up to 12,000 bu/hr can be realized.
​
In nearly all cases, a rotary motion obtains the highest possible throughput of product per unit of screen area. As the particles travel down the sieve, the rotary motion allows for lateral, diagonal and longitudinal separation through varying screen openings and layers. With rotary action, the particles are exposed to a greater number of screen openings per pass, as compared with reciprocal motion. By utilizing the latest available technology, CNSSC has set a new standard in rotary screen separation. The NS Series of high-quality, rotary screen cleaners is truly today’s leader in capacity, versatility and performance.


Flow, Deck & Screen Combinations
There are two basic flow combinations for the new NS Series rotary screen cleaners: parallel flow for high-capacity applications, and counter flow for more precise separations where increased screen retention time is required. Out of these two basic flows are many variations of scalp/sift combinations that allow the NS Series of rotary screen cleaners the flexibility to meet all customer needs in capacity,
​
Standard Features
-
Structural components made from heavy-gauge steel
-
Stress relieved
-
Orbiting screen action for superior screen capacity
-
Parallel or counter-flow deck configurations
-
Low-maintenance suspension rods and heavy duty universal joints
-
Heavy-gauge internal spouting for enhanced wear resistance
-
Positive securing of screen frame to shoe
-
Uniframe screen construction to ensure correct dimension between ball & screen, allowing maximum cleaning action
-
Inspection doors & sampling ports
​
Option
-
Additional rough scalping or fine scalping capabilities on one of the following:
-
Standard rubble deck
-
Extended rubble deck
-
Double extended rubble deck
-
-
5° or 7° pitch shoes on selected models
-
Open and closed circuit scalper aspirators
-
Open and closed circuit aspirators
NS Rotaries: P33 Series
Complementing the NS 88 & 120 Series rotaries, the P33 Series can provide either in-line resifting functionality with the P33 LS Series or multiple scalping functionality with the P33 TS Series. This additional functionality is achieved without compromising machine capacity. This new feature reduces traditional shrink associated with cleaning operations and also provides a “value-added” marketing opportunity. This feature also provides the ability to clean multiple commodities without having to change screens. This flexibility results in less down time. The P33 Series Rotary has become an important part of Northland’s innovative In-Line “value-added” grain processing philosophy.



Aspirators
Aspirators provide an effective solution for dust, fines and chaff removal. Two basic models are available: Open Circuit, which uses the external dust control system to provide a fresh air supply; and Closed Circuit, which uses integral fans to provide a supply of recirculated air. In both models the air supply is pulled through the product stream to lift and separate fines from the product mass. NS Aspirators are available in widths from 24″ to 115″ and in various body styles.
Options
Fixed- or variable-speed feed rolls for uniform feed rate and positive shut-off on selected models


Closed Circuit
-
Closed Circuit Aspirators use recirculated air from internal fans to separate or lift materials from the product mass.
-
Recommended usage is for primary or secondary cleaning applications containing 2% or less fines.
-
Typical applications: wheat, barley, oats, canola, corn, rice, pulse crops, edible beans, soybeans, sunflower, safflower, mustard, sorghum, etc.
-
Capacities variable with physical characteristics of incoming product, outgoing specifications, scalper mesh size, moisture content and operating efficiency.
-
Proper setting of the air control adjustments is critical in optimizing performance of the Aspirator.

Open Circuit
-
Open Circuit Aspirators require a remote dust control system to remove air separated materials.
-
Recommended usage is for all applications in a pre-cleaning or primary cleaning environment where large amounts of fines are present.
-
Typical applications: wheat, barley, oats, canola, corn, rice, edible beans, soybeans, sunflower, safflower, mustard, sorghum, etc.
-
Capacities variable with physical characteristics of incoming product, outgoing specifications, scalper mesh size, moisture content and operating efficiency.
-
Proper setting of the air control adjustments is critical in optimizing performance of the Aspirator.
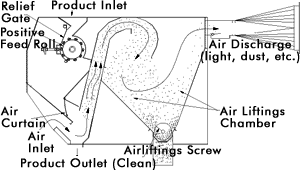
Destoners
For cost-effective removal of stones
An integral component of Bjerke Brothers, Inc.‘s in-line grain cleaning system is the NS-DS-24 CC Destoner. The destoner is typically placed in the grain flow after the combination length and width separator. Its function is to remove stones, iron, fertilizer granules, dirt, glass and other heavy foreign materials from grain. The primary function of the destoner is to separate this unwanted material prior to the grain flow entering the thresher.
In operation, the NS-DS-24 CC Destoner separates foreign material from the grain by gravity. Grain enters the destoner at the product inlet. The grain is then elevated by upward air pressure generated from the fan. The heavy material (stones) falls through the air stream and is discharged from the machine. The grain that is elevated continues upwards. The heavier grain falls into the first settling chamber and the lighter grain continues to the second chamber to be discharged.
Standard Features
-
Closed circuit-integral fan
-
Feed bar
-
Sampling ports
-
Counter-weighted product discharges
-
Air bleed-in control
-
315 C.F.M. negative air port
-
Magnehelic gauge for static pressure monitoring
-
Enclosed machine design
-
Adjustable fan damper
-
Two-coat Hammertone green machinery enamel paint
​

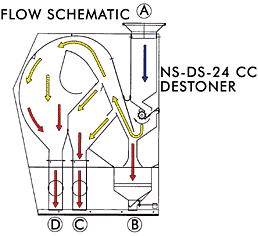
Threshers
Bjerke Brothers, Inc. is proud to present its lineup of versatile and robust wheat head threshers; models ET-16 and ET-20. An integral part of our industry-leading “in-line wheat cleaning system,” the ET Series thresher simply and effectively processes and recovers wheat from unthreshed wheat heads. When used in conjunction with Crippen Northland Superior’s wheat head destoner, a typical operation will recover in excess of 70% of wheat by weight from the wheat heads. Payback from your investment in the form of additional revenues from a newly created long position on wheat stocks commences immediately with many systems completely paying for themselves in the first year.
A unique feature of Bjerke Brothers, Inc.‘s Thresher ET-16 design is its ability to perform the dual function of a debearder. By changing the drive and slowing down the RPMs of the inner drum, customers are able to debeard barley, clip and polish oats and de-awn durum. This saves in both floor space and additional equipment costs.
The ET Series threshers essentially consist of a dynamically balanced inner drum rotating within a heavy-gauge, abrasion-resistant outer casing. The inner drum and inside casing of the housing are lined with hard-surface beater bars. The space between the opposing beater bars is factory set and does not require operator intervention or adjustment. Wheat heads enter into the thresher at the inlet hopper and are conveyed and forced through the constricted space between the beater bars. The threshed wheat and chaff are discharged from the machine for further separation on existing cleaning equipment. Processing efficiency can be controlled by adjustments on the weighted discharge gate, thereby altering the flow rate of the product through the thresher.
​
The ET-16 thresher features a 16″ inner drum and is ideal for light to medium applications. The ET-20 thresher is designed for the most demanding of application
​
Standard Features
-
Dynamically balanced drums for vibration-free operation
-
(ET 20) Heavy-gauge, abrasion-resistant housing
-
Removable end plates
-
ET 20 Series features 20″ rotating drum c/w replaceable hard-surface beater bars on inner drum
-
ET 16 Series features 16″ rotating drum of solid one-piece construction
-
Low-maintenance poly belt drive system
-
Simple and easy to operate
-
Enclosed machine design
-
Counter-weighted discharge gate
​
Options
-
Motor and Horsepower Specifications
-
Aspiration Discharge Spout


Combo Cleaners
CNSSC NS Series of Combination Cleaners is part of a new generation of grain and oilseed processing equipment. Used in an in-line cleaning system, a terminal reclaim line or as a stand-alone specialty cleaner, the Crippen Northland Superior combination cleaner offers both versatility and reliability. The combination cleaners are offered in a wide variety of configurations to suit the customer’s needs.

Indent Cylinder Length Separators
Bjerke Brothers, Inc. supplies indent cylinder separators in configurations from one to 30 cylinders, and capacities from 60 to 6,000 bu/hr (1.6 to 163 tonnes/hr).
High-Capacity Multi-Cylinder Cleaners
Bjerke Brothers, Inc.‘s NS Series is the industry’s leading line of indent cylinder length separators, and offers a full range of sizes, capacitiesand configurations to meet every length separation application. With a modular design and two cylinder sizes – the NS-B and NS-S Series – numerous variations are available, with capacities ranging from 160 bu/hr up to 6000 bu/hr.
​
Rigid enclosed frame construction and poly belt chain drives provide smooth, vibration-free performance with low energy consumption. Manufactured to the highest standards, all Crippen Northland Superior Indent Separators require only routine maintenance to ensure years of trouble-free operation. All parts subject to wear are readily accessible and easy to replace.
​
The rotating 23″ or 17″ diameter indent cylinder, case-hardened for optimum life, is the key component of the NS series separators. Available in a wide range of indent pocket sizes, NS cylinders can remove large or small material as desired to meet every separation requirement.
​
Simple operating adjustments allow for a wide variation of products to be separated by the NS Indent Cylinder Separators. The separating edge (A) can be raised or lowered, allowing the receiving trough (B) to catch desired liftings of shorter grains as they drop free from the cylinder indents (C). Turning the hand wheel (D) adjusts the position of the separating edge, with the pointer (E) showing the position on the indicator dial (F). The inspection door (G) allows observation of the cylinder separation process.
​
The liftings are transported out of the receiving trough by a screw conveyor. Grain line blades (H) connected to the bottom of the trough ensure a steady grain flow along the length of the indent cylinder. The flow of the unlifted longer material (tailings) exiting the cylinder is controlled by the adjustable retarder blade (I).
.jpg)
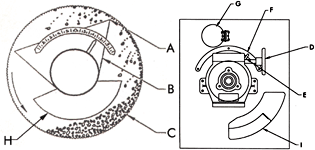
Standard Features
-
Two basic cylinder diameters: 23″ (NS-B) or 17″ (NS-S)
-
Long-wearing case hardened and reversible cylinder shells
-
Indent pockets available in wide range of sizes
-
Receiving trough adjustment for precise separation; dump position for complete clean-out
-
Retarder adjustment to maintain desired grain level
-
All controls accessible and easy to operate
-
Dual-drive configuration for five-row-high models
-
Poly drive belts for smooth performance and long life; no lubrication; maintenance-free
-
All wear components are readily accessible and easy to change
​
Options
-
Custom spouting configurations
-
Stainless steel, ceramic or urethane spouting liners for longer life
-
Cross screw conveyors from discharge spouts
-
Actuator-controlled trough adjustment
-
Chrome-plated cylinder shells
-
Cylinder wear bands
Modular Design
Multi-cylinder arrangements from one to 30, up to five high and six wide, provide complete flexibility to meet any application.


Choice of Various Flow Options to Suit All Separation Requirements
Parallel flow is characterized by the same product flow directions for each cylinder row. From a main spout, the product is equally distributed to cylinder rows from one side of the machine.
​
Series flow allows for multi-separation from one stream and is characterized by the counter-flow directions of the separated product for each cylinder row. The product enters the first cylinder row and flows back through the row below.

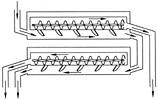
Parallel and Series Flows May Be Combined in One Machine

Single-Cylinder Seed Cleaners
The new NS-SC Seed Cleaner is designed and manufactured by Crippen Northland Superior for accurate separation of any commodity on the basis of length difference.
​
The modular design allows the NS-SC to be used individually or arranged as a multiple-cylinder machine. A variety of interconnecting spouting arrangements provides for a wide range of flows.
​
The NS-SC separator is a simple, single-cylinder machine utilizing a main drive, conveyor shaft and cylinder as the only moving parts. A 17″ diameter cylinder, hardened for optimum life, is the primary component of the NS-SC. The size of the indent pockets on the inside surface of the cylinder determines the length of the lifted material. Any material the same size as or smaller than the indent pockets is lifted and dropped into the receiving trough. The transportation of the material from the trough to an outside spout is performed by a screw conveyor. The remaining larger material is taken to the discharge spout by grain line blades connected to the outside bottom of the trough.
​
A 1/2 H.P., 1800 RPM motor mounted inside the body of the machine allows variable speed through a V-belt drive and reducer.
Great Flexibility
Indent cylinders are available in many sizes to suit a wide variety of separation needs. Variation in separating performance can be achieved by several easy adjustments.
-
Cylinder speeds variable from 35 to 60 RPM
-
Wide range of trough angles
-
Retarder control for grain depth
All controls are within easy reach of the operator.
Easy Cylinder Change and Cleaning
The NS-SC separator is easily and quickly cleaned.
-
machine can be mounted on a slight incline to allow faster cleaning
-
removable doors give easy access to the cylinder compartment for easy cleaning and maintenance
-
optional split cylinder construction allows fast replacement of cylinder
-
Crippen Northland Superior’s advanced surface hardening process ensures the cylinders are both long-lasting and round.
-
The universal design of Crippen Northland Superior’s cylinders enable them to be used on other manufacturers’ 17″ cylinder machines.
Easy Operation and Maintenance
Simple construction and smooth, vibration-free operation are factors making the NS-SC separator very efficient in all aspects of operation and maintenance. The NS-SC separator is solidly constructed, and only routine maintenance is required to ensure years of trouble-free operation.
Standard Features
-
Adjustable retarders
-
Trough locking mechanism
-
Motor mounted inside the frame of the machine
-
Trough adjustment for complete clean-out
-
Dust control connection at the discharge end for dust-free operation
-
Variable-speed operation
​
Options
-
Location of the cylinder speed handwheel at the discharge end
-
Feeder providing uniform feeding
-
Spouting kits for stacking machines in parallel or series flow
-
Lined infeed casting
-
Split cylinder shells



Modular Design
Any number of complete modules can be put together in a series flow (to reclean either liftings or tailings) or parallel flow for maximum capacity.

Internal Drive

Machine Specifications
A wide range of simple operating adjustments allows for variation in the product to be separated. The separating edge (A) can be raised or lowered, so the receiving trough (B) catches desired liftings as they drop free from the indents in the cylinder (C). This adjustment can be set by turning the handwheel (D) which causes the pointer (E) on the indicator dial (F) to be moved. To build up and maintain the desired grain level, the retarder can be positioned by using the counter weight (G). The inspection opening (H) allows observation of the separation process taking place inside the cylinder. If necessary, the cylinder speed can be regulated during operation by turning the handwheel (I).


Scalper Aspirators
Bjerke Brothers, Inc. Scalper Aspirators are designed and manufactured to provide two main product separations. The first separation involves scalping or removing large unwanted materials from the product streams. The second separation removes fines from the product stream by use of the controlled air flow through the product stream. Crippen Northland Superior Scalper Aspirators are engineered for use in the harshest of conditions in continuous operations.
Two basic models are available; Open Circuit, which uses the external dust control system for air supply and Closed Circuit, which uses integral fans for air supply. Various options, including scalper roll screens in wire mesh sizes from 5/8 to 1 1/4″ center to center, rolled into 12″, 18″ or 24″ diameter, and incremental lengths from 36″ to 115″ long, provide for a wide range of available capacities and operating efficiencies.
Standard Features
-
Wire mesh or punched-flat metal scalper roll screens in a wide variety of sizes
-
Adjustable air bleed-in
-
Maintenance-free sealed bearings
-
Poly belt drives
-
Closed or open circuit
-
Air liftings discharge from either LH or RH of machine
-
Adjustable feed gate
-
Aspiration velocity control
​
Options
-
Fixed or variable speed feed rolls for uniform feed rate and positive shut-off
-
Feed inlet agitator
-
Feed roll cavity spacers for precise volume control
-
Stainless steel product contact areas for product flow lubricity
-
Abrasion liners on selected impact areas


Closed Circuit
-
Closed Circuit Scalper Aspirators use recirculated air from internal fans to separate or lift materials from the product mass.
-
Recommended usage is for primary or secondary cleaning applications containing 2% or less fines.
-
Typical applications: wheat, barley, oats, canola, corn, rice, pulse crops, edible beans, soybeans, sunflower, safflower, mustard, sorghum, etc.
-
Capacities variable with physical characteristics of incoming product, outgoing specifications, scalper mesh size, moisture content and operating efficiency.
-
Proper setting of the air control adjustments is critical in optimizing performance of the Scalper Aspirator.
-
Rescalping Reel available on 24″ Scalper Aspirators. Consult factory for dimensions.

Open Circuit
-
Open Circuit Scalper Aspirators require a remote dust-control system to remove air-separated materials.
-
Recommended usage is for all applications in a pre-cleaning or primary cleaning environment where large amounts of foreign materials or fines are present.
-
Typical applications: wheat, barley, oats, canola, corn, rice, pulse crops, edible beans, soybeans, sunflower, safflower, mustard, sorghum, etc.
-
Capacities variable with physical characteristics of incoming product, outgoing specifications, scalper mesh size, moisture content and operating efficiency.
-
Proper setting of the air control adjustments is critical in optimizing performance of the Scalper Aspirator.
-
Rescalping Reel available on 24″ Scalper Aspirators. Consult factory for dimensions.
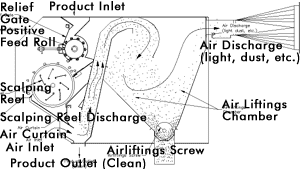